RRD Facility Spotlight: RRD Packaging Solutions – Durham
12/16/2021 RRD
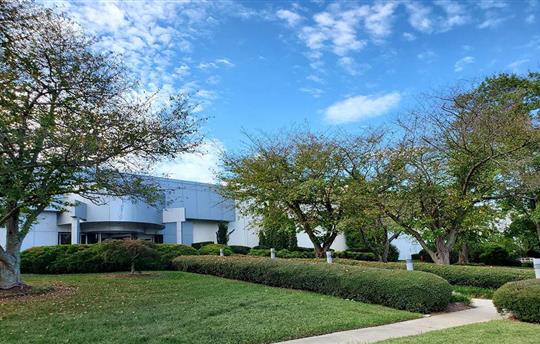
RRD Packaging Solutions – Durham (formerly known as PBM Graphics) is a leading packaging manufacturer strategically located in North Carolina’s Research Triangle. This facility provides a litany of services that include design engineering, basic to complex folding carton production, turn-key trading card game production, complementary commercial print services, as well as sophisticated kitting or light-assembly and fulfillment operations.
With a campus spanning over 450,000 square feet, RRD Packaging Solutions – Durham ensures its clients the opportunity to produce all of their needs in a one-stop environment that is highly controlled and continuously improving.
To learn more about this facility’s expansive material applications, efficient processes, and unmistakable company culture, we connect with four individuals who have a lot to do with its ongoing success: Jim Hummer, VP of Operations; Dean Robinson, SVP of Operations; Ryan Vinyard, Director of Operations; and Mark Davis, Director of Client Services.
What is it about RRD Packaging Solutions – Durham that makes it unique in the current marketplace?
Jim Hummer, VP of Operations: I know “one-stop-shop” can be a bit overused in our industry, but it’s a phrase that accurately represents what this facility is truly capable of. Durham produces, stores, and ships what our clients need, when they need it.
To get a little more specific, I think it makes sense to drive some attention to our specialty equipment — and we have a rarely seen full complement of it. This machinery enables us to create truly unique, high-grade packaging through the application of extraordinary embellishments.
Our eight and 12-color UV presses have multiple coaters, which provides great range and efficiency when it comes to applying varnishes and other unique coatings (e.g., spot and reticulating, soft touch, and metallics). We’re also set up to provide embossing, high-end foil stamping, and die cutting as well as production of foil board for our folding carton clients. I should also mention we also have a blister coating press on-site.
Again, this is an impressive roster of equipment that you’ll be hard pressed to find elsewhere under one roof.
If you had to narrow it down to one, what do you consider Durham’s forte?
Dean Robinson, Senior Vice President: Our ability to manage complex packaging programs to a very high standard is one of the greatest strengths at Durham. Capacity and scaling power are key to making that possible.
We have Fortune 500 and world-class manufacturing clients with wide-ranging product sets that require large volumes and unique embellishments. In total, this is an over 450,000-square-foot multi-building facility; our massive capacity allows us to do everything in-house with minimal outsourcing. For our clients, that translates to greater consistency, intellectual property security, on-time delivery, and improved accountability.
To maintain this standard of excellence, we continue to meet the requirements for a number of certifications (i.e., G7, ISO 9001, FSC, SFI, PEFC, and Lean Six Sigma). We’re also audited by our clients regularly to ensure we’re meeting their own specific requirements.
Can you share a recent success story that showcases this capability?
Ryan Vinyard, Director of Operations: Actually, what’s happening right on the production floor is essentially a success story. We’ve instilled the Lean Six Sigma culture at Durham to systematically improve our team’s performance and maximize efficiency.
This Lean approach has enabled us to offer shorter lead times than ever before because our processes flow very efficiently.
Durham has also implemented an ERP system for packaging, which has streamlined operations, allowing us to monitor waste and improve inefficiencies in production. These changes add value to our processes and result in improved quality and reduction in lead times. With efficient processes, we are better able to meet our customers' demands.
The team is embracing the Lean methodology and culture change with a focus on being a world class operation. We all have a role to play to keep our operating cost down, produce best-of-class-quality and maintain a safe working environment.
When talking about the Durham facility to a current or potential client, what’s the one thing you find yourself repeating time and time again?
Mark Davis, Director of Client Services: I think it’s really important to emphasize what our clients see when they walk into our Durham facility.
Quick story: We’re currently working with a midsize U.S. company with a portfolio of more than two dozen personal care brands. They’ve turned to RRD for our folding carton solutions; we’re producing more than 12 individual structures for over 60 active SKUs. During a recent plant tour, the client’s procurement specialists and packaging engineers saw RRD efficiency first hand. And it resonated with them because it matched their own facilities in cleanliness and organization.
When our clients walk through the door here, again, they see cleanliness and confidence in our people running fine-tuned processes. And when they see it’s such a tightly run ship, I have to believe they intuitively infer that errors are going to be rare, with almost non-existent incompletions or missing product.
The reality is world-class clients expect world-class service. So we don’t have a choice but to bring our best into this facility every day. We're proving it through KPIs and continuous improvement factors. The Durham team has worked so hard for the credibility we’ve earned and the growing opportunities we have to protect our clients’ brands is a testament to that.
For more information about this facility, visit the RRD Packaging Solutions – Durham location page.