RRD Facility Spotlight: Brno
1/2/2024 RRD
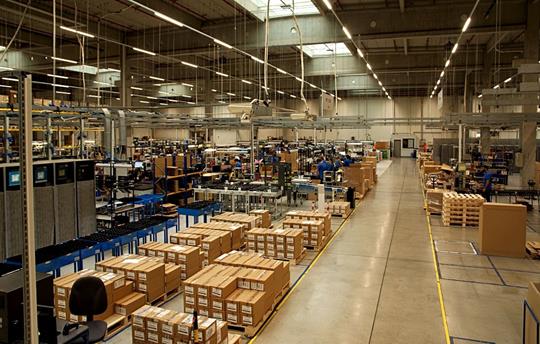
Located in the heart of Central Europe, RRD’s expanded Brno, Czech Republic facility boasts an impressive 15,000-square-meter footprint and provides a large range of services, including:
- Supply chain network analysis and solution design
- Project management
- Procurement and inventory management
- In-region device configuration
- Advanced testing and software re-flashing
- Kitting, distribution, and fulfillment
- Reverse logistics and spares services
RRD Brno complements RRD’s wider European offering of environmentally sustainable print, digital print, and packaging solutions. Neil Keleher, RRD Brno’s Senior Vice President of European Operations, shares some insight into how this leading facility has enabled companies to consolidate suppliers and optimize costs.
What about RRD Brno makes it unique in the current marketplace?
Neil Keheler (NK): It comes down to the range of services RRD Brno is capable of. From sourcing, kitting, and assembly to finished product fulfillment, we are strategically positioned to provide a vertical solution for our client's products — and enable fast access to the European market.
In leveraging RRD's global production assets and Brno’s assembly and fulfillment operations, our clients benefit from a complete product supply chain solution and extensive quality assurance, which is an integral part of our workflow.
If you had to narrow it down to one, what do you consider to be RRD Brno’s forte?
NK: Europe is not homogeneous — there is a lot of complexity in the products and markets of each country. Support for this level of complexity can only come from a partner that can fulfill multiple language product versions in near real-time.
I would say our forte is managing the complexity that arises from supporting our customers’ multiple requirements — all in a seamless manner. Our clients have various direct and indirect requirements, from brand and product protection to the management of specific country regulations and multi-channel fulfillment.
Brno’s extensive supply chain capabilities provide a single interface for all of these requirements, helping companies reduce complexity and refocus on core business activities.
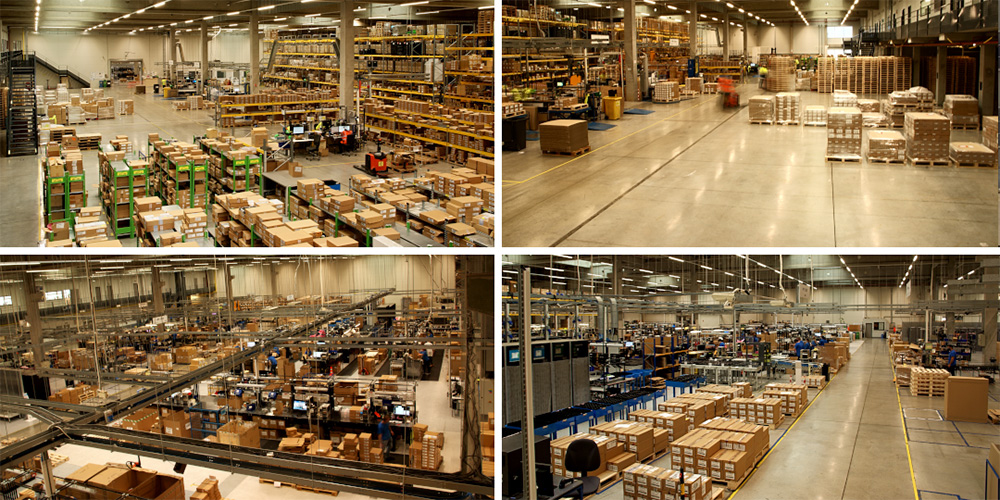
As business evolves, what role do you see RRD Brno playing in that evolution?
NK: I think you will start to see companies adopting a control tower supply chain model — which is something RRD Brno specializes in — and realize that a single interface for their supply chain can become a true competitive advantage.
Additionally, RRD’s global footprint works alongside our European platform of vertically integrated design, print, packaging, device assembly, and kitting resources. This will continue to help companies mitigate risk by nearshoring elements of their supply chain.
RRD is a partner to some of the world’s leading medical device companies and as part of our investment in this sector, the Brno facility now has ISO 13485:2016 accreditation. Our goal is to further serve the needs of medical device clients throughout Europe.
We are also in the process of expanding our operational space to an impressive 15,000 square meters. This expansion emphasizes our steady commitment to delivering outstanding services and quality to our valued clients. The new space provides us with opportunities to streamline processes, optimize services, and enhance support. We are always attuned to the needs of our client base, and this expansion will enable an increased capacity, allowing us to handle larger volumes of orders and provide even faster delivery times.
Can you share a success story that showcases RRD Brno?
NK: We recently developed an in-region postponement solution to drive efficiencies across the entire supply chain for a global consumer electronics and mobile device company. Previously, the company had imported their finished rugged phones from multiple Chinese original device manufacturers (ODMs), which created a number of difficulties around forecasting, flexibility, product ramp-up, and branding.
To get around these issues, we consolidated all printing, packaging, device configuration, and testing to a centralized European distribution center and provided the ability to track each product by serial number. This eliminated the inefficiencies created by shipping finished goods for the European market directly from China.
By working through RRD Brno, the company was better positioned to support their international customers in EMEA and also significantly reduce freight and storage costs. (Read the full case study here.)
Step inside RRD's Brno facility on a Virtual Plant Tour here. For more information about RRD's supply chain services, head here.