How Playing 20 (or More) Questions Can Improve Labeling Performance
2/16/2021 Bill Gonio
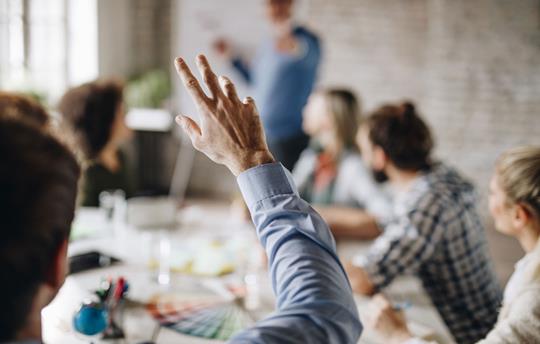
When working with labels, engineers have a surprising number of things they need to consider to ensure they work properly and last for the right amount of time. Whether your label includes safety information or instructions, the importance of making sure it is applied correctly and remains on the product is a continuing struggle.
Every stage of the labeling process requires your attention, and it’s sometimes hard to know where things have gone wrong when it doesn’t work properly.
Looking for more insight on label performance?
Get to know RRD's 2021 Industrial Labels Toolkit.
Was it applied incorrectly? Are the materials of lower quality? Are you using the wrong adhesive for the substrate?
Trading basic questions like these (and many more like them) with your labels provider is the best way to avoid issues from the manufacturing stage to many years after.
When it comes to label problem solving, avoid complicating the process. Your labels provider should keep things simple and collaborate with you to answer the essential questions, from start to finish.
1. Start at the beginning
Begin with the possibilities that are determined by your requirements. Most of these will be questions about compliance and regulations regarding your label:
- Are there any environmental label design requirements?
- Does the EPA or CPSIA restrict certain materials?
- Is the surface area where the label is applied textured, rough, oily, painted, curved?
- Do labels need to be UL certified?
- Will the product be outdoors? Underwater? If so, for how long?
- Will the product be subject to extreme temperatures?
- How long does the label need to remain on the product? A day? Ten years?
- Will the label be a fire hazard if applied in the wrong place?
- Do you completely understand the end use of the product receiving the label?
These are the questions that solidify your concrete constraints, which are the elements of a label that cannot change and need to be considered when creating a label constriction.
2. Refine the selection process
Then proceed to the questions that refine your selection process based on design and product specs. An example of this includes identifying the type of material(s) used in the product’s label application surface. This helps determine:
- Effectiveness of the adhesive (is the label meant to be removable?)
- The different shape of the application surface or products
- Different locations for placement, size, and thickness
Additional label application criteria involve where you work. Labels require clean environments and stable temperatures in order to be applied correctly. Are you applying labels in a cold area? Are there large amounts of dust in the air? Leaving these questions unanswered can often affect the long-term performance of the adhesive.
3. Save questions around preference and price for last
From there, proceed to questions regarding preferences and price. This may include colors, printers, label material (plastic, fabric, etc.), whether the label is in one piece or multiple, and so on. Most of these questions are based on your personal working preferences, or what the designers want to see.
These should not be determined until all of the other questions I’ve brought to your attention first are addressed. If you’re figuring out the color of the label before you know where it’s going or what it’s going to say, then you’re only creating a headache for yourself later.
Access your copy of RRD's 2021 Industrial Labels Toolkit.
Generally, most problems with label compliance come from a process that is being rushed or wasn’t thought all the way through.
Are your labels discolored after just a couple of days?
Are they falling off after a few minutes in the fridge?
Are they wrinkled after application?
If so, odds are an important question has not been asked (or answered). Taking the time today to ask all the right questions — at every step of the labeling application process — will save you time and effort later.
Remember: To improve performance, understand your label’s problem before you start fixing it. To do so, ensure you're working with your labels provider to ask (and answer) the right questions.
Bill Gonio is a Regional Quality Manager for RRD Label Solutions.