5 Keys to Continuous Improvement in Labeling Application
2/16/2021 Craig Black
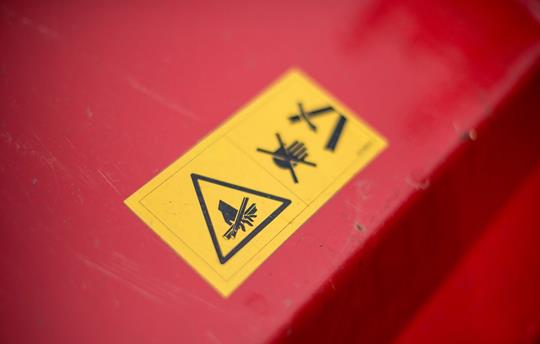
There’s no shortage of challenges when it comes to improving labeling productivity:
- Products requiring many labels
- Product variations requiring different versions of the same label
- Lack of automation requiring manual application
- Vague understanding of the labeling process
- Limited feedback from operators on their application challenges or ideas
Because labeling productivity is rarely considered as an opportunity for continuous improvement, the incentives and savings to change go undetected for companies. An unfortunate result is that most labels are designed primarily for function with minimum consideration of the labeling process.
To overcome these downstream challenges, there are five best practices every engineer should employ.
Looking for more insight on label performance?
Get to know RRD's 2021 Industrial Labels Toolkit.
Evaluate your labeling applications, periodically
This includes getting input from the production floor. Test any variations in output and production speed. Conduct studies to determine any efficiency improvements such as jigs/guides for faster, more accurate label placement.
If you are using manual labor where automation can improve both the quality and output, it may be time to build a case for implementing automation, such as dispensers that are semi-automatic or applicators for higher speeds. When this is done, engineers typically report a positive ROI.
Identify ways to improve the initial design of labels
Can labels be finished on rolls for quicker removal? Does the design contribute to the overall efficiency of the labeling process? In the new product design process, durable labels are often created by cutting and pasting previous designs as the last parts for the bill of materials.
Taking extra time to rethink productivity during the label design stage may help improve your production later.
Convert preprinted labels on the production floor to print-on-demand
Print-on-demand labels are blank labels printed by thermal printers. This conversion reduces SKU count, handling, and inventory costs and increases the amount of variable data on the labels. It opens up opportunities for barcoding, QC codes, or other security features that may help support both the supply chain and the customer experience.
Design and implement label kits for durable products
Label kits are sheets that contain multiple labels for one item number, instead of sourcing separate labels for the same item and printing labels on separate sheets at different times.
Kits are effective solutions that eliminate touch points, provide quality control, and alerts you if any labels have been omitted on the product. They maintain color and material consistency and provide efficiency in applying your labels.
Label kits can even be adapted for assembly-line labeling or for finishing areas where all labels are applied at the same time.
Every label has a purpose — know it
No matter what your goal for improvement is, keep in mind the intended purpose of the label.
Is it for decoration, instruction, or safety? Does it present static information, variable data, or a combination?
If you have a clear understanding of the label’s purpose, you will be able to identify its properties that can change, and where you should focus your attention.
While every labeling process is unique, basic considerations like these are great starting points when you want to improve your productivity and reach your production goals.
Craig Black is a Sales Executive for RRD Label Solutions.